Construction Equipment Management Software
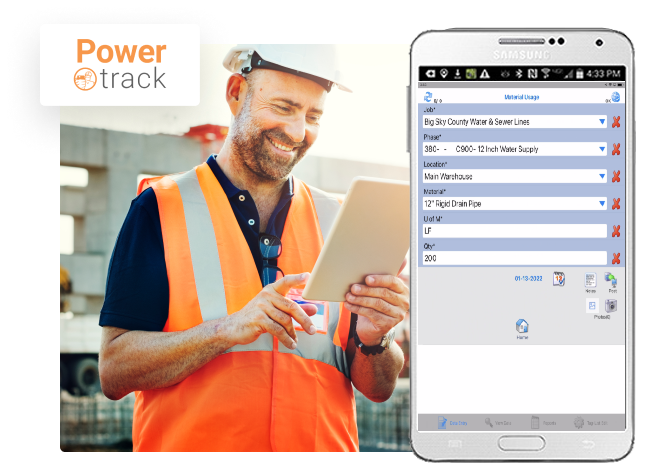
Construction Equipment Management Software & Tool Tracking System
- Improve equipment management by tracking equipment usage, movement, and much more
- Track material and tool inventory usage on job sites
- Track small tools and manage tools issued to a job and returned from a construction site
- Use barcode scanning to track tools, equipment, and materials
Add Mobility Tracking to Your Accounting/ERP System
For construction professionals using Trimble Construction One, Viewpoint Vista, Viewpoint Spectrum, and SAGE 300, PowerTrack has the integrations to track your assets.
Material, Tool, and Equipment Inventories Management
What if you do not have a current enterprise asset management system? No sweat. You can use PowerTrack’s solution for tracking and managing tools, equipment, inventory and material.
- Increase accountability with asset tracking
- Option to use barcodes to increase proficiency and accuracy
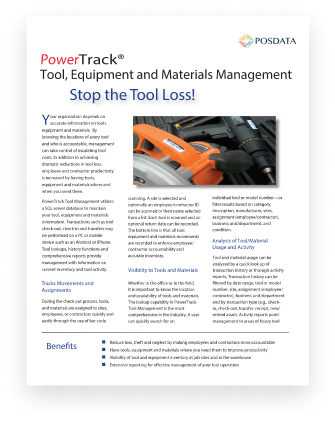
Track Movements and Assignments
During the checkout process, assigning tools, equipment, and materials to employees or contractors is done quickly and easily through the use of barcode scanning. An employee/contractor ID is scanned, or a name is selected from a list. A job site or other location can be selected. Each tool is scanned, and a return date can optionally be recorded. Tools can also be transferred between locations without an employee/contractor assignment. The result is that all asset movements are recorded to enforce employee/contractor accountability and accuracy for your entire inventory.
Visibility to Tools and Equipment
Whether in the office or the field, it is important to know the location and tool availability. The tool lookup capability in the PowerTrack Tool Management system is one of the most comprehensive in the industry. You can quickly search on an individual tool or model number—or filter results based on the manufacturer, description, category, assignment (employee/contractor), site, business unit/department, or condition.
Analysis of Tool and Material Usage and Activity
Tool and material usage can be analyzed by a quick lookup of transaction history or through activity reports. Users have the ability to filter transaction history by date range, tool or model number, assignment (employee/contractor), site, business unit/department, and transaction type (check-in, check-out, transfer, new/retired asset). Tool data and activity reports can point management to areas of heavy tool utilization or tools that are rarely used, thereby guiding maintenance schedules and future tool purchases.
Schedule Your Demo Today
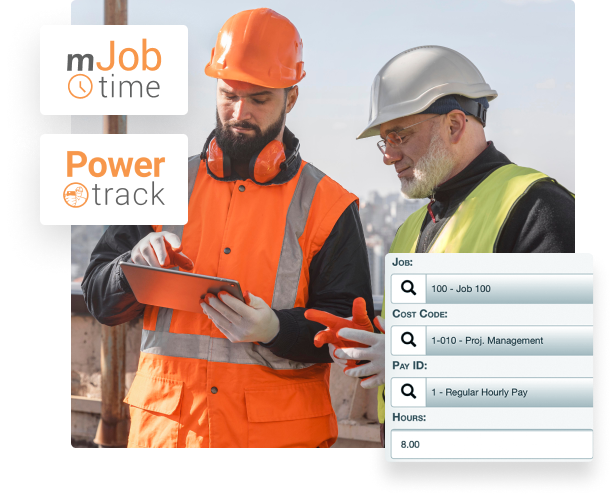